
The cyanide effluent is oxidized with alkaline chlorine to nitrogen and carbon dioxide, using sufficient added caustic soda to give pH 9.5–10, again with a HRT of around 20 min. The chromic acid (Cr 6) is pretreated by reduction to chromate (Cr 3) using sulfur dioxide gas or sodium bisulfite along with sulfuric acid to give an operating pH below 2.4, with a hydraulic retention time (HRT) of around 20 min.

They are treated in opposite ways, one under acidic reducing conditions, the other under alkaline oxidizing conditions, in both cases under the control of redox probes. These effluents must be treated separately because, if they were combined, they would release cyanide gas. Thus two waste streams are produced: an alkaline cyanide effluent and an acidic chromate effluent, each containing traces of the base metals which were immersed in them.
#Chromium plating free
The pretreated parts are then plated in a chromic acid bath and subsequently rinsed free of surplus plating solution in running water. Seán Moran, in An Applied Guide to Water and Effluent Treatment Plant Design, 2018 Case Study: Plating EffluentsĬhromium plating requires that the metal to be plated is immersed in a sodium cyanide/caustic soda solution as a pretreatment, after which it is rinsed free of alkaline cyanide in running water, producing a rinse tank overflow contaminated with alkali and cyanide. Nevertheless, platinized titanium anodes have been recommended for some types of fluoride-free high efficiency plating solutions in which the standard lead/ tin anodes have been found to dissolve too rapidly. However, no oxidation of Cr(III) occurs at its surface. Platinized titanium has also been suggested as a more suitable material for this purpose, and indeed does remain uncorroded. The use of lead and iron is therefore now almost entirely confined to that of auxiliary anodes. While the rate of dissolution of iron anodes depends on their purity, Armco iron, for example, being relatively slowly attacked, no ferrous anode is as efficient as lead for the re-oxidation of trivalent chromium. However, both tend to dissolve too rapidly, with the former becoming readily coated with lead chromate and the latter leading to an increase in the iron content of the solution. Pure lead and iron have been used as anodes in the past. This must be removed either by physical means or chemical dissolution before the desired peroxide film can be re-established 135. If the lead alloy anodes are left idle for long periods in the chromium plating solution, an electrically insulating layer of lead chromate forms on them. Kagan and Bonnemay 134 have studied the effect of anodic oxidation with the use of radioactive tracers. This feature can be used to advantage to re-oxidize excessive quantities of Cr(III) by using a piece of scrap metal having a small surface area as cathode while maintaining a large anode area.
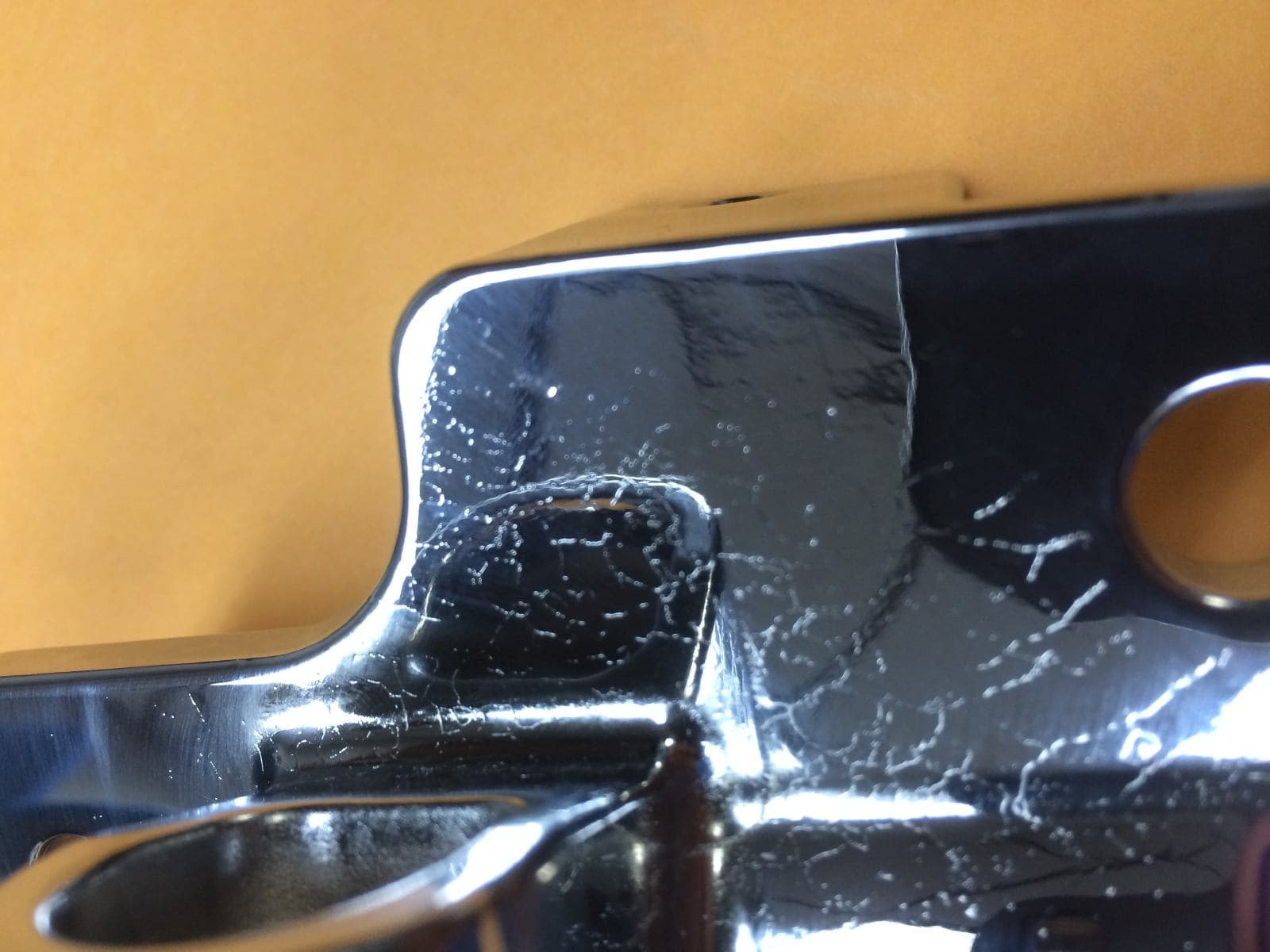

This will result in an equilibrium being set up between the cathodic reduction of Cr(VI) and its anodic oxidization with the resultant concentration of Cr(III) depending on the relative cathode and anode surface areas. In this condition, they will reoxidize much of the Cr(III), formed at the cathode, back to Cr(VI). When operating correctly, these anodes should be coated with a chocolate brown film of lead peroxide (PbO 2) 132, 133. The lead-tin alloy was found to be more resistant, and being also suitable for chromic acid baths containing sulphate only, has now largely superseded the antimonial lead type as the common anode material. The former alloy was once used exclusively, but when fluoride-type catalysts were introduced it was found that it was corroded rather severely. These are lead alloys containing 6–8% antimony or 4–6% tin 29. Such, in Nickel and Chromium Plating (Third Edition), 1993 AnodesĪnodes of chromium metal would neither be economical to manufacture nor technically advisable for chromium plating baths, for they would dissolve at approximately 100% efficiency and hence rapidly increase the chromium content of the baths.
